12/3/2014
BY DEBRA THIMMESCH
Just in case you missed it. Here's a helpful tip for patriots and survivalists...
source
BY DEBRA THIMMESCH
Just in case you missed it. Here's a helpful tip for patriots and survivalists...
One of the obstacles to jumping headlong into the additive manufacturing milieu for many people is often the expense of the 3D printer itself. Further, for those intrepid, budding engineers, designers, makers, and artists, an initial foray might more reasonably and affordably involve
using a less expensive and complex machine. Enter one Instructables contributor, “mikelllc,”who has designed a make-it-yourself 3D printer that is constructed largely from recycled electronic components.
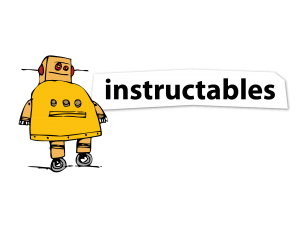
Currently, only about 12.5% of all electronic waste, or “e-waste,” is recycled. Instead, the majority of cast-off electronic products — around 20 to 50 million metric tons per year worldwide — end up in incinerators or landfills. Many such products languishing in landfills can also release toxic chemicals into the air and soil, including high amounts of lead. So, repurposing electronic products makes great sense economically and ecologically.
The EWaste $60 3D Printer is inexpensive to make given that you can round up the necessary components and follow the maker’s step-by-step instructions, which are clear and detailed. The process, in short, involves schooling yourself on “how a generic CNC (Computer Numerical Control) system works” and then programming your printer-in-the-making to respond to G-code instructions. With the addition and calibration of a plastic extruder, the tuning of the driver power, and other well-outlined and described steps in the construction process, you end up with a “small footprint” 3D printer that is comprised of upwards of 80% recycled components — an eco-conscious and budget-friendly alternative to springing for a new and potentially costly 3D printer.
One of the major selling points of this design for a 3D printer is that not only do you end up with a usable machine at the end of the process, but that the process of building and programming the thing yourself also provides you with a solid tech-ed mini-course (or maxi-course for the completely uninitiated). What you need to get started are two standard CD/DVD drives from a used PC, a floppy disc drive from which you extract stepper rather than DC motors (you’ll need three stepper motors in all), a PC power supply, cables, female connectors, a heat-shrink tube, and some CNC electronics. There are some components — like a NEMA 17 stepper motor — that you’ll need to purchase new, but for the most part you’ll be going with used and recycled parts.
The Instructables page provides thorough instructions for everything from soldering the cables to the motors and doing the basic electrical work, installing and using Arduino printer control software, downloading firmware, configuring the motherboard, and so on. In the instance of components that are not accessible from previously used electronics, there are instructions and templates for making your own laser cut parts for the frame, which can be assembled without the use of glue.
The 3D printer uses 1.75 mm plastic filament, which is both easier to extrude and also much more flexible than 3 mm filament. Additionally, using the 1.75 mm filament means that you’ll require less power to run your machine, which is definitely earth-friendly, as is the use of PLA bio-plastic (as opposed to ABS). This maker is willing to be contacted for troubleshooting, and the project — and completely usable end result — seems worth the fairly complicated process.
Is this a project you’d think to undertake? Have you already? Let us know how you found the process, and what your results were, at the discussion forum for the EWaste $60 3D Printer at 3DPB.com!
source
No comments:
Post a Comment